What is EPDM?
EPDM stands for Ethylene Propylene Diene Monomer.
EPDM is an exceptionally strong, flexible and long-lasting synthetic rubber.
Why is EPDM so reliable?
EPDM is resistant to water, steam, cold (down to -40°C), heat (over 200°C), sunlight and ozone.
EPDM is highly effective in numerous applications; especially where structures, equipment and personnel require weather and safety protection or electrical insulation.
Applied in the right ways, EPDM delivers long-term performance and protection, every time.
How is EPDM used?
Wherever you are and whatever you’re doing, EPDM is probably not too far away!
EPDM is commonly used for window and door seals (buildings and vehicles), fridge and freezer seals, automotive hoses, windscreen wipers, water pumps, engine cooler tubes, fan belts, solar panel heat collectors, speaker cone surrounds, vehicle bumpers and playground surfaces. To name just a few.
EPDM is used to make automotive hoses
EPDM is used to make windscreen wipers
EPDM is used to make playground surfaces
EPDM is used to make speaker cone surrounds
Why is EPDM a great material for flat roofing?
EPDM is exeptionally tough, airtight and weathertight.
EPDM remains impervious to heavy rain and baking sun, puncture resistant and highly elastic for several decades.
It looks smart too.
Read on to find out how FlexiProof EPDM membranes are specially made with the best raw materials for robust and long-lasting flat roof protection.
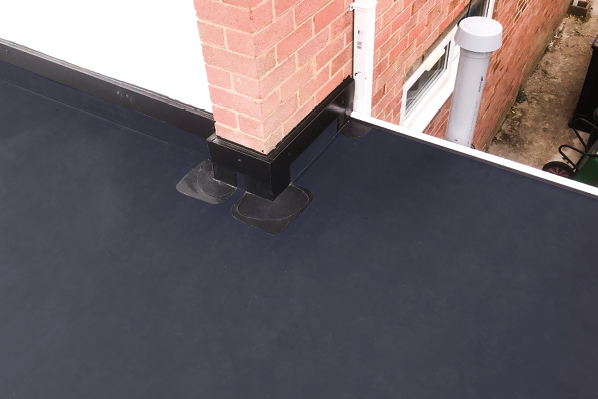
How are FlexiProof flat roof EPDM membranes made?
The best raw materials
FlexiProof EPDM compounds are made up of four main ingredients:
• EPDM polymer
• Carbon Black
• Paraffinic oils (used as softeners)
• Fillers/activators/crosslinking systems
Two-ply EPDM sheets
Single sheets of FlexiProof EPDM membrane are formed by heat-laminating two uncured plies of EPDM (with a taffy-like consistency) together during the extrusion process.
Imperfections are eradicated and watertight toughness is assured.
EPDM master rolls created with ‘homogeneous’ joins
FlexiProof EPDM membrane sheets are initially produced at a maximum size of 10ft x 50ft (500sq ft).
Using heat and pressure, the sheets are fused together to create lengthy master rolls whilst the EPDM is still uncured (and tacky).
EPDM master rolls cured for high-performance
Uncured master rolls of EPDM are loaded into huge, pressure cooker-like units and cured under heat and pressure.
The uncured EPDM becomes thermoset EPDM, making it extremely durable and resilient.
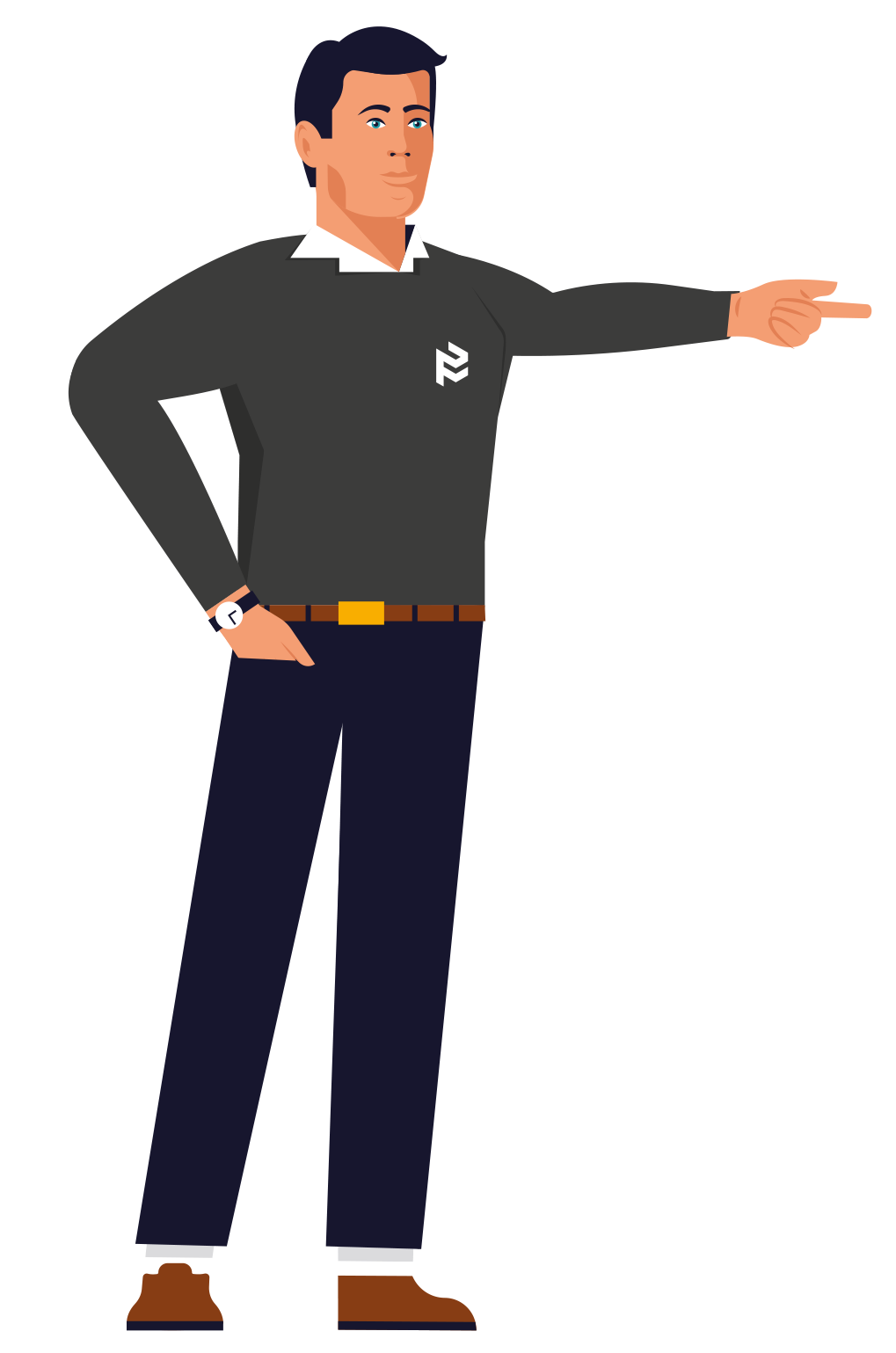
“Using heat and pressure, the sheets are fused together to create lengthy master rolls whilst the EPDM is still uncured (and tacky).
The ‘joins’ invisibly fuse together to create homogenous sheets of EPDM. ”
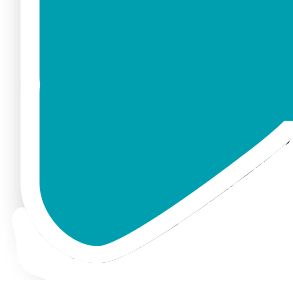
Flat roof success for all
Made with the right materials and processes, EPDM is the perfect material for successful flat roof projects.
The EPDM compounds, extrusions and manufacturing processes used to create FlexiProof One Piece and Fleece Backed EPDM membranes are carefully selected and maintained to deliver long-term flat roof success.
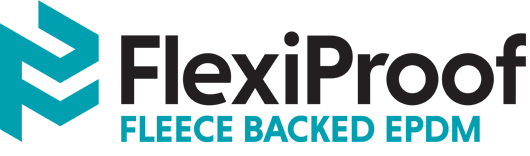
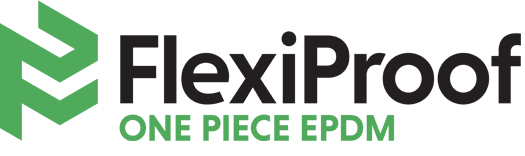